Company Advantages1. The design team has been researching Rocket PCB
printed circuit board manufacturing with innovations, keeping up with the trends.
2. The overall quality of this product is ensured by our professional QC team.
3. Our quality inspectors make sure that the product is in accordance with international quality standards.
4. The product has significant development advantages compared to other product.
5. The product has won the common recognition since its wide application prospects have been praised by many customers.
Capabilities involved in PCB backplane design
CCL
Because the thickness of the backplane, size and is not the same as a conventional board, its performance requirements for the CCL is not the same
Thickness
The thickness of the backplane is thicker than that of the conventional board
Size
The size of the backplane is much larger, for production also has this certain impact
Drilling
Due to the increase in thickness and the use of crimp contact, the accuracy of drilling and the ability to copper plating has special requirements
The number of layers
The layer of the backplane also be developed to the high-level number, more than 10 layers of design is also more common.
Layout
Backplane wiring density is relatively small, but there are special requirements for impedance requirements and inner-layer lines.
Surface treatment
Due to the thickness of the backplane, size is relatively large, some surface treatment process is more difficult to achieve
Special process
Due to the characteristics of the backplane itself, the backplane sometimes uses some special processes.
In Rocket, with advanced production equipment, excellent PCB solutions
and complete testing methods, we have specialists working on their
particular fields with the thorough mastery of their particular
discipline in each of the production facilities. Training, as well as
technical exchanges, are held frequently, tackling problems in key
technologies and configuring scheme of equipment and allowing
professionals to get up to speed on the essential tools that many
organizations value today in the manufacturing industry. Thanks to those
above, we have greatly improved the strength and won international
reputation.
SPECIALIZED MANUFACTURING
Conductive materials and core-to-core bonding
Embedded components
RF connector attachment
Laser direct imaging (LDI)
Laser etching
Laser forming
Multi-level cavity construction
Plated cavities and edges
Composite/hybrid Structures
N+N dual press-fit
Dual-drill
Bonding on metal core
Bulid-up HDI
Long-short and staged gold finger
CAPABILITIES
3mil line and space
4mil laser defined vias
6mil chip-on-board
6mil mechanically drilled vias
Conductive and non-conductive via fill
Dual backdrilling
Sequential lamination
Mixed dielectric
Heatsink Bonding
Heavy copper/thermal vias
Blind/buried vias
Stacked and staggerd microvias
EXTENSIVE ANALYTICAL TESTING
Design Rules Check(DRC)
Electrical Testing
Automated Optical Inspection(AOI)
X-Ray
Plating thickness testing
Metalized vias inspection
Thermal shock testing
Surface peelability testing
Impedance control testing
100% visual inspection
Solderability testing
Ionic cleanliness testing
Metallographic microscopic analysis
High voltage testing
Insulating resistance testing
FEATURES
PTFE
High speed/low loss
High temperature
Low CTE
Lead-free, HASL, ENIG, EPENIG, Immersion Silver, Tin, Gold finger
Combination surface finished
Copper-filled microvias
Advanced Product and Technology
bg
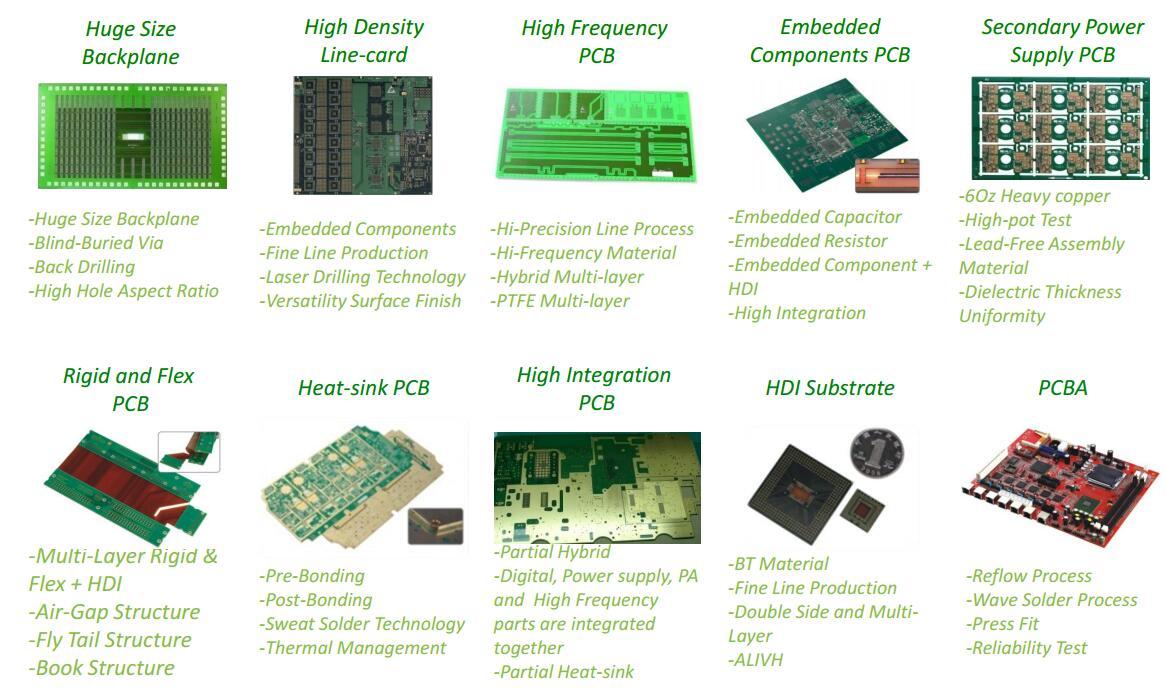
High-speed Backplanes:
◪ Panel sizes up to 54 inches
◪ Over 70 layers
◪ Blind and back drilled through holes
◪ Dual diameter holes
◪ Heavy copper layers
◪ Connector expertise
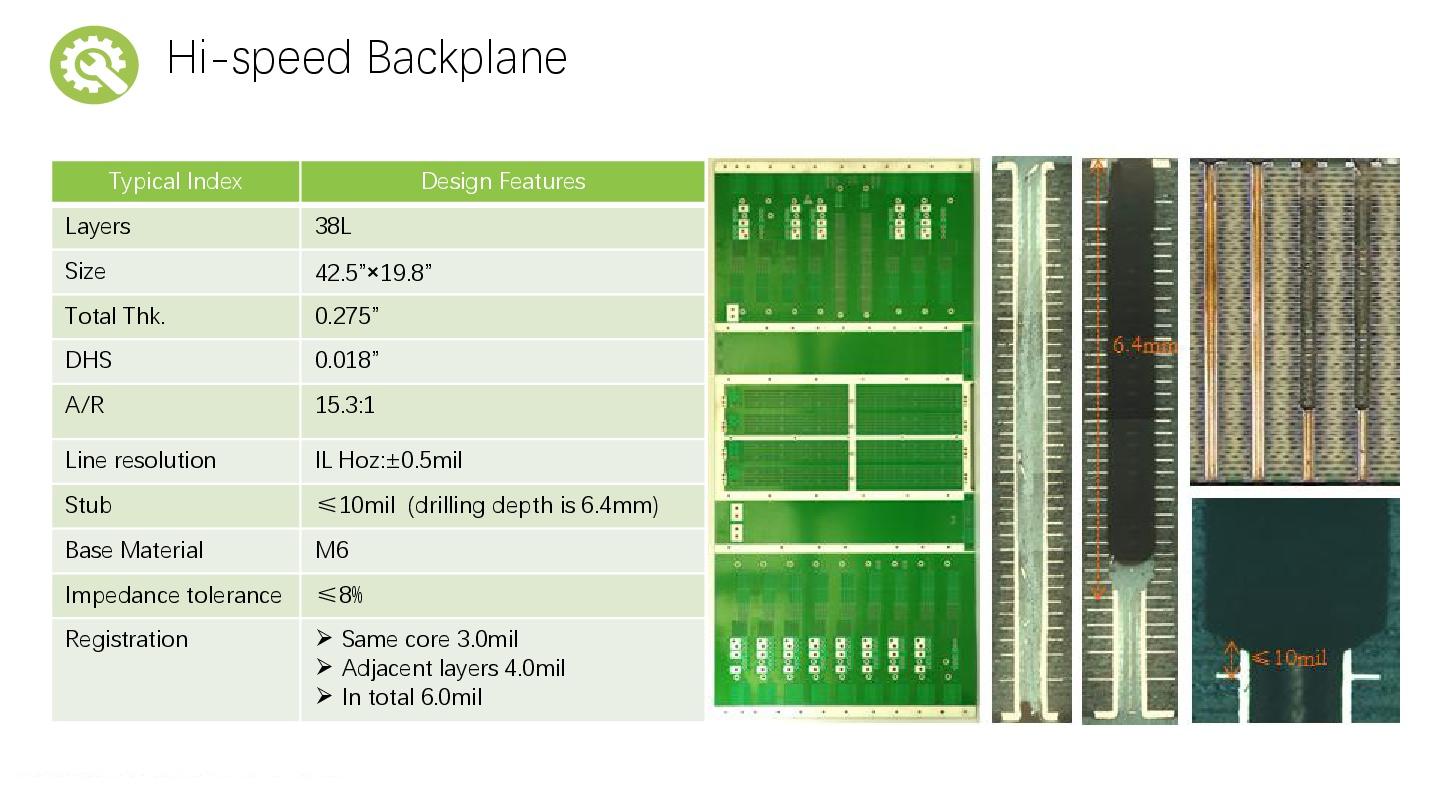
24 hour real-time technical support Quick turn around with 24 hours and
instant quote. For Backplane board, will be based on board parameters,
normally 15-30 days.
Effective and flexible PCB engineering solutions save your cost. We always put
the best interests first when providing innovative solutions for
manufacturing customers’ products, we are more willing to help customers grow.
Rapid feedback on the layout,build-up, panels,
impedance, material selection, design rules, manufacturability,
costs of different solutions, use of micro vias, gold plating, special
laminates, etc.
Strong partnerships with different reputed material suppliers such as Rogers, Arlon, Nelco and Taconic can realize a fast service to a wide
range of PCB applications.
Dozens of tests such as open/short
circuit testing( ET test), AOI, X-ray, impedance testing, solderability
testing, thermal shock testing, metallographic micro-slicing analysis,
halogen-free testing, etc.100% outgoing pass rate.
Complete services from free DFM, traceable manufacturing to complete after-sales service, on time delivery 99%.
We will keep secret for customer sale area, design ideas, drawing and all other private information.
Flexible payment terms. Samples for 100%TT, mass production payment: 50%
advance payment 50% balance should be paid off before loading or accept
monthly statement if the order is stable.
Consumer electronics
Automotive electronics
Communications
Energy
Industrial & Instrumentation
IOT/Smart Home
Medical electronics
Security Industry
Company Features1. Rocket PCB Solution Ltd. has proven over time to be an outstanding supplier of high-quality
Backplane PCB that is both consistent and predictable.
2. We employ a team of exceptional R&D talents with deep experience. They are engaged in the research and development of the products while keeping up with the market trend.
3. Rocket PCB Solution Ltd. can promise that we will try our utmost to satisfy our customers. Get info! Our culture of high speed backplane enables us to look forward to working with customers to create a brilliant future together. Get info! A central tenet of Rocket PCB Solution Ltd. could be summarized as printed circuit board manufacturing . Get info!